Recognizing the Fundamentals and Applications of Plastic Extrusion in Modern Production
In the world of modern manufacturing, the strategy of plastic extrusion plays an instrumental duty - plastic extrusion. This intricate process, involving the melting and shaping of plastic via specialized dies, is leveraged across different sectors for the production of diverse items. From car parts to durable goods product packaging, the applications are large, and the capacity for sustainability is similarly remarkable. Unwinding the principles of this procedure discloses real flexibility and capacity of plastic extrusion.
The Fundamentals of Plastic Extrusion Process
While it may appear complex, the basics of the plastic extrusion process are based upon relatively simple principles. It is a manufacturing procedure where plastic is melted and after that formed right into a continual account via a die. The raw plastic material, commonly in the form of pellets, is fed into an extruder. Inside the extruder, the plastic goes through warmth and stress, causing it to thaw. The molten plastic is then required through a shaped opening, called a die, to create a long, continual product. The extruded item is cooled down and after that reduced to the desired size. The plastic extrusion procedure is extensively utilized in various markets due to its cost-effectiveness, flexibility, and performance.
Different Kinds of Plastic Extrusion Methods
Building upon the standard understanding of the plastic extrusion process, it is required to discover the different strategies included in this manufacturing approach. In comparison, sheet extrusion creates big, level sheets of plastic, which are typically additional refined right into products such as food packaging, shower curtains, and auto components. Comprehending these methods is crucial to making use of plastic extrusion properly in modern manufacturing.

The Function of Plastic Extrusion in the Automotive Industry
A frustrating bulk of parts in contemporary vehicles are items of the plastic extrusion procedure. This procedure has reinvented the automobile market, changing it into a much more efficient, affordable, and versatile manufacturing field. Plastic extrusion is primarily used in the manufacturing of various auto elements such as bumpers, grills, door panels, and dashboard trim. The procedure supplies an attire, consistent result, enabling suppliers to produce high-volume components with wonderful precision and minimal waste. The lightness of the extruded plastic look at here now components adds to the general decrease in car weight, improving gas effectiveness. Furthermore, the resilience and resistance of these components to heat, chilly, and effect improve the long life of cars. Thus, plastic extrusion plays a pivotal duty in vehicle production.

Applications of Plastic Extrusion in Consumer Goods Production
Beyond its substantial impact on the automotive industry, plastic extrusion proves just as efficient in the realm of customer goods manufacturing. The convenience of plastic extrusion enables producers to make and create complicated shapes and dimensions with high accuracy and effectiveness. The flexibility, flexibility, and cost-effectiveness of plastic extrusion make it a recommended choice for numerous customer items makers, adding considerably to the market's growth and innovation.
Environmental Effect and Sustainability in Plastic Extrusion
The prevalent use of plastic extrusion in producing invites analysis of its environmental ramifications. As a procedure that regularly makes use of non-biodegradable products, the ecological influence can be considerable. Power usage, waste production, and carbon emissions are all concerns. Market advancements are enhancing sustainability. Effective equipment reduces energy usage, while waste monitoring systems recycle scrap plastic, decreasing resources needs. Additionally, the development of naturally degradable plastics offers a get more much more eco pleasant choice. Despite these enhancements, additionally development is needed to alleviate the ecological impact of plastic extrusion. As culture leans towards sustainability, suppliers must adjust to remain sensible, emphasizing the importance of continual research and development in this area.
Conclusion
Finally, plastic extrusion plays a vital duty in modern production, specifically in the automotive and durable goods fields. Its adaptability permits for discover here the manufacturing of a variety of elements with high precision. Its possibility for recycling and growth of biodegradable materials provides an encouraging opportunity towards sustainable practices, thereby resolving ecological concerns. Understanding the basics of this process is key to maximizing its applications and advantages.
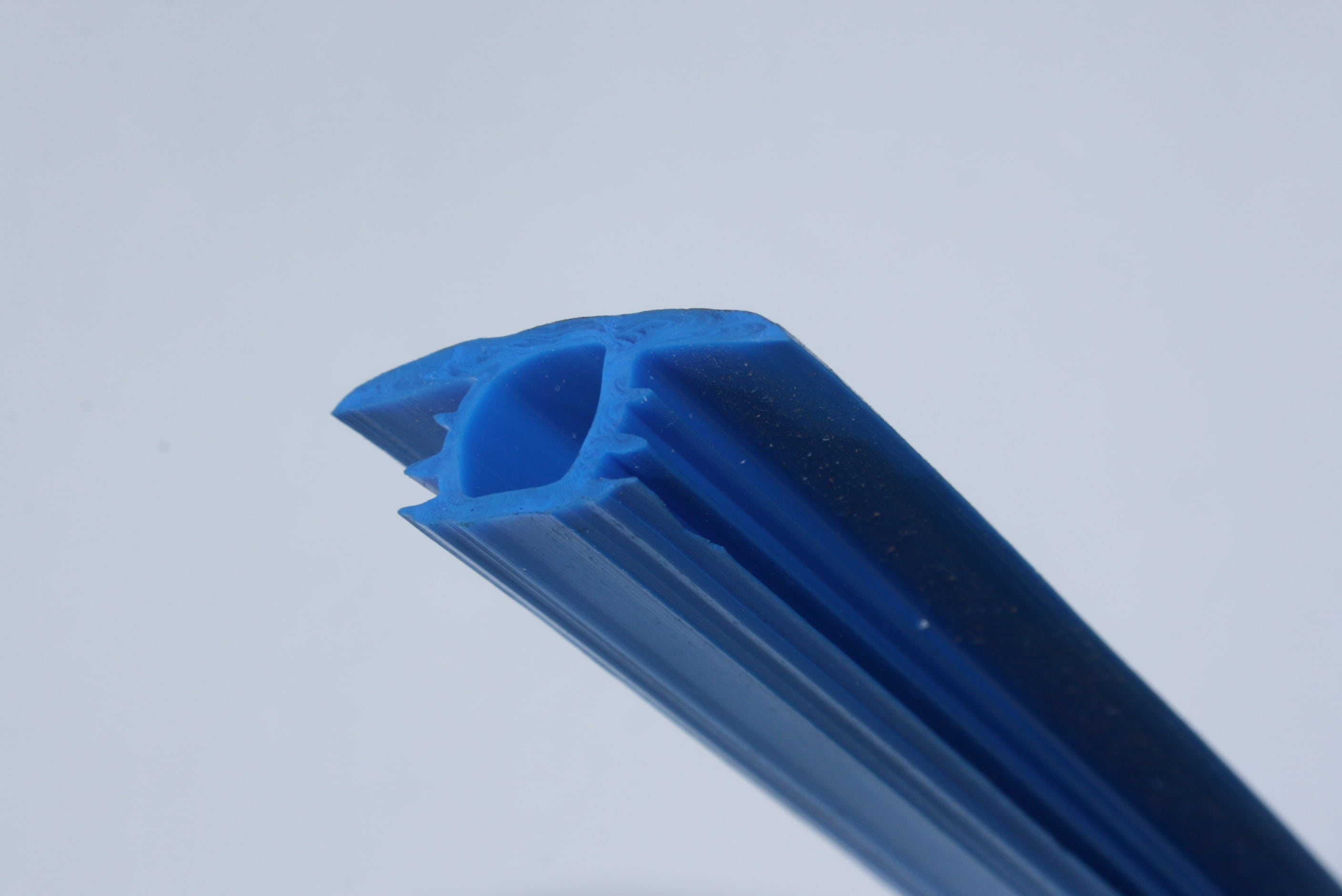
The plastic extrusion process is thoroughly used in different markets due to its efficiency, flexibility, and cost-effectiveness.
Building upon the standard understanding of the plastic extrusion procedure, it is necessary to discover the different techniques included in this production technique. plastic extrusion. In contrast, sheet extrusion produces large, flat sheets of plastic, which are normally further refined right into items such as food packaging, shower drapes, and auto parts.A frustrating bulk of parts in contemporary lorries are items of the plastic extrusion procedure